Accumulator
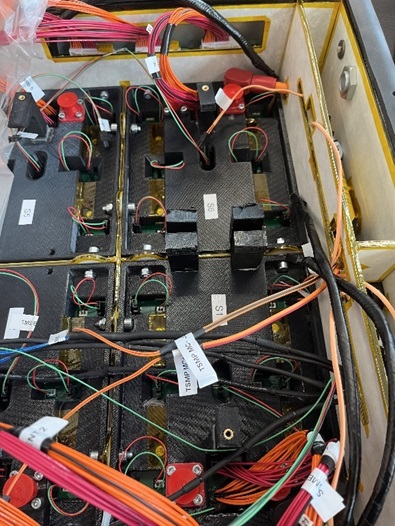
The Accumulator Mechanical sub-team designs the enclosure for the energy storage system of the car that delivers high current to the motors during acceleration and driving. The objective of this enclosure is to protect the battery from the outside environment, allow for safe and convenient access to its electronics, while minimizing both weight and cost, and maximizing packaging efficiency. On this sub-team you’ll work closely with the electrical sub-team for safety and assembly considerations. Also, you’ll work with the chassis sub-team on its mounting position, which determines the center of mass of the car, and strategy that makes the Accumulator easy to take in and out of the car. Overall, you’ll learn electromechanical integration strategies, and how to apply them while optimizing your weight, cost and packaging efficiency.